HVAC designers today must consider both air quality code requirements spawned by ASHRAE Standard 62 (Ventilation for Acceptable Indoor Air Quality), and operating cost considerations. Variable air volume (VAV) systems are an effective solution for reducing both the first cost and operating costs for a building owner. Maintaining proper outside air dilution rates, air motion and air distribution becomes the challenge for the VAV system designer.
An airflow sensor in each VAV terminal measures the flow of conditioned air and sends a differential pressure signal to a controller. The accuracy and range of the airflow sensor and controller are critical to the system’s ability to control airflow, outside air dilution and air motion at part-load conditions.
THE PROBLEM:
Design For Part-load and Full-load Conditions
Until recently, accurate airflow measurement at or near minimum airflow conditions was considered less important than thermal comfort. However, today maintaining proper minimum airflow setpoints is a primary concern to ensure proper ventilation in the occupied space. Even with sophisticated air diffusers, accurate airflow control is necessary to maintain proper air throws required for proper air diffusion within the space.
HVAC system designers select VAV terminals for minimum pressure drop and noise, which often results in oversized terminals. These minimum design airflows can result in differential pressure signals below the range of control for VAV controllers. One of the following two problems results:
- Excessive airflow at the actual minimum setpoint exceeds the design minimum setpoint, causing overcooling of the space. Terminals with heating coils will be energized pre-maturely, wasting energy.
- Inadequate ventilation and discomfort occur due to zero airflow in lieu of the minimum design capacity.
Undersizing VAV terminals to accommodate typical airflow sensors results in higher pressure drops and sound levels, increased energy consumption and noise in the occupied space.
Conventional Airflow Sensors Cause Problems
- Typical airflow sensors only measure accurately with ideal inlet duct conditions. Anything other than straight inlet duct will cause the airflow calibration curve to shift or change in slope, requiring field calibration.
- Any movement of the flexible duct at a terminal unit’s inlet will change the airflow sensor calibration, changing the airflow setpoints.
THE SOLUTION:
Accurate Airflow Measurement Permits Proper Ventilation and Stable Temperature Control
Successful VAV systems demand airflow measuring sensors that can accomplish the following:
- Provide accurate and repeatable airflow measurement, regardless of inlet duct configurations.
- Develop an amplified velocity pressure signal at low air velocities to allow proper terminal sizing at full load, and accurate minimum airflow operation at part load.
- Accomplish these tasks without increasing sound levels or pressure drop.
Airflow sensors should traverse the inlet duct using methods outlined in the ASHRAE Fundamentals Guide. Pressure measurements should be taken in equal cross sectional areas, or by using the log-linear traverse method along two perpendicular diameters (Figure 1). The number of pressure measurements should increase with the inlet collar size and be no fewer than six measurements per diameter (12 total sensing points).
Center Averaging is the Key
The airflow sensor must average all the discrete pressure measurements instantaneously in a pressure collecting chamber located in the center of the sensor (Figure 2). Low velocity pressure on one side of the duct and high velocity pressure on the opposite side is averaged together in the center pressure collecting chamber before being output to the controller. Center averaging is the single most important characteristic required for accurate airflow measurement. Without this feature, the output pressure signal reflects the pressure measurement closest to the controller, rather than the average differential pressure within the duct.
Amplifying the Airflow Sensor Signal Allows Lower Minimum Airflow Setpoints
Many VAV controllers require a minimum differential pressure signal of 0.03 inch w.g. The airflow sensor should be able to generate this signal with only 400 to 450 FPM air velocity through the inlet collar.
Conventional airflow sensors without amplification capabilities require approximately 700 FPM to generate a 0.03 inch w.g. signal. If 700 FPM represents a 20% minimum condition, the inlet velocity would be 3500 FPM at the maximum airflow setpoint. This results in extremely noisy conditions. In addition, the airflow sensor should generate a differential pressure range of at least one inch w.g. over the operating range of the terminal unit.
Some Airflow Sensors Adversely Affect Noise and Air Pressure Drop
Some airflow sensor designs amplify the velocity by enlarging the sensor face area (Figure 3). This method amplifies the velocity pressure in two ways:
- The static pressure immediately behind the sensor is reduced by substantially obstructing the airflow pattern.
- The free area of the inlet collar is considerably reduced by the large face area of the sensor. The resulting higher air velocity generates a higher velocity pressure.
This method of amplification has the following negative side effects:
- Higher terminal sound levels.
- Increased pressure drop, increasing central fan power consumption.
ENVIRO-TEC Patented Its Breakthrough Airflow Sensor, the FlowStar™
ENVIRO-TEC’s patented FlowStar airflow sensor amplifies the velocity signal without increasing the unit air pressure drop and noise. The sensor features center averaging for maximum accuracy under all conditions. The face area of the sensor has been minimized and an airfoil hub is used to minimize turbulence, pressure drop and noise generation. The velocity pressure signal is amplified 2.5 to 3 times, providing accurate and repeatable airflow rates to the occupied space through a conservatively sized VAV terminal.
The performance of the VAV terminal airflow sensor is a key factor in successful HVAC system design. It is imperative that the designer give this aspect of the job design and specification sufficient attention in order to meet both indoor air quality and operating cost objectives for today’s buildings.
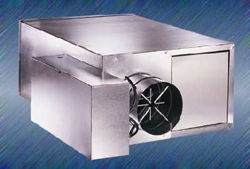 For maximum indoor comfort, specify CFRQ extra quiet fan powered terminals. This constant volume terminal provides higher air motion and better air distribution in the occupied space. The FlowStar airflow sensor permits adequate ventilation in the space. This combination provides the ultimate in zone comfort control.
Suggested Airflow Sensor Specification
The VAV schedule should specify the minimum and maximum airflow setpoints, maximum sound power levels, and maximum air pressure loss for each terminal. The specification for the VAV terminal must detail the required performance of the airflow sensor. For maximum building occupant satisfaction, the VAV system designer should specify the terminal unit airflow sensor, as shown below.
Differential pressure airflow sensor shall traverse the duct using the equal cross sectional area or log-linear traverse method along two perpendicular diameters. Single axis sensor shall not be acceptable for duct diameters 6" or larger. A minimum of 12 total pressure sensing points shall be utilized. The total pressure inputs shall be averaged using a pressure chamber located at the center of the sensor. A sensor that delivers the differential pressure signal from one end of the sensor is not acceptable. The sensor shall output an amplified differential pressure signal that is at least 2.5 times the equivalent velocity pressure signal obtained from a conventional pitot tube. The sensor shall develop a differential pressure of 0.03" w.g. at an air velocity of < 450 FPM.
Retrofitting a Building to Meet New IAQ Standards
The FlowStar sensor is available as a stand alone airflow measuring station. The Model RFT-MS (right) is a short circular sheet metal sleeve that can be easily attached to any VAV terminal that has a round inlet. The old sensor can be removed and the FlowStar then connected to the existing controller.
Due to the accuracy of the FlowStar, air balancing does not require time consuming duct traverses. The RFT-MS is provided with field balancing taps and an airflow calibration chart. Maximum and minimum airflow setpoints can be quickly calibrated using a differential pressure gauge.
Visit the RFT-MS web page here.
Top of Page |